Dielectric materials are an important consideration when designing and producing PCBs. They influence both the mechanical and electrical properties of the PCB which is more and more important in the fast moving PCB industry.
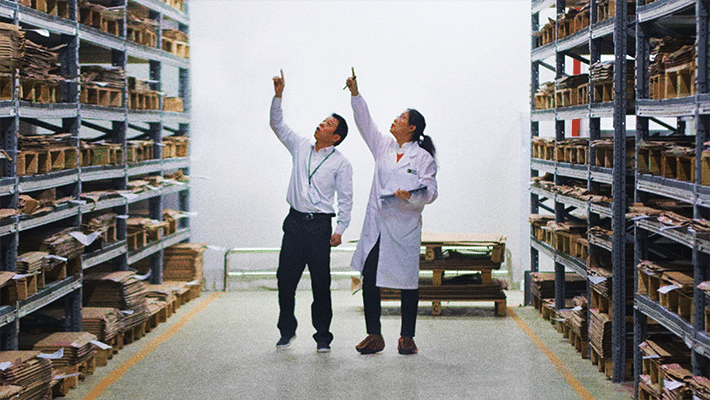
As features such as blind and buried vias, multilayer HDI stack-ups and high frequency signals become more common, the dielectric materials used in production need to be carefully selected to ensure the PCB operates to its highest potential.
Material Producer
The material producer refers the company that produces the specific material you want to use, for example, Dupont, Isola and Shengyi. This becomes important when considering the type of board you wish to create. High-tech prototype PCBs and complex HDI builds are often ordered through western PCB producers, where higher volume series production is often ordered through manufacturers in China. This is important because PCB suppliers in different regions have different standard material producers that they use. Specifying a Western-originated or European/US based material for a series production in China could lead to long lead times and delays in production. When you are planning to go for the volume production to China we could advise you in your material selection.
Datasheets and Key Values
Datasheets for PCB materials are often easily accessible online through a simple google search of the material type. They can be quite confusing to look at as there are large amounts of information that you may not understand. To make this easier I will outline some key values to look out for.
First is the Tg value. This is the glass transition temperature which indicates at what temperature the base material will become unstable. Common Tg values to specify are 130, 150 and 170 degrees Celsius. It is important to consider this because if your PCB will be operating in a hot environment, then specifying an appropriate Tg could increase the longevity of the PCB. It is also wise to consider the Td value of the material as well. This refers to the decomposition temperature of the material caused by the resin. It is often presented in a data sheet in a table along with the Tg value and other material properties.
In addition to thermal properties it is also important to look at the electrical characteristics of the materials such as the Dk value, the dielectric constant. This is especially important to look at if you have a design with high speed signals which requires controlled impedance traces. When you have defined this you need a certain impedance value for your single ended or differential pairs it is advisable to indicate the Dk value. When you have indicate the Dk value it supports the PCB manufacturing to simulate the outcome of the impedance value with the given stackup. Finally we will look at the CTI value. CTI stands for comparative tracking index and is a measure, in voltage, for the breakdown of a material. It is commonly presented as a PLC unit which is a simplified scale of voltage ranges as seen in the table below.
So how to choose material for your PCB?
3 key rules to consider:
What do you require in construction
UL approved in factories
Considering lead time, materials that are too specific
Let´s take an example to select your material: High layer count material selection for Mid-Tg lead free material. Definition:
Mid-Tg means 150°C <Tg< 170°C;
Compared to normal Tg, thermal performance of mid-Tg is better especially in the lead-free process; compared to high-Tg material, basically the price of mid-Tg is competitive;
Here, high layer count means layer count >=8L.
Talking about mid-Tg material, normally we will check information of Tg, reliability such as thermal stress cycles, anti-CAF, ease of purchase and price level.
Selection:
Many material suppliers have mid-Tg material. The widely used ones are SY,EMC, ITEQ, and Panasonic.
The prior recommendation for mid-Tg lead-free material is S1000H and IT-158. Both of them can pass 4 times sequential lamination.
Be sensitive to the differences. For example a ShengYi mid-Tg material has differences between a S1000 and S1000H.
For halogen-free material requirements, you may select R-1566(WN), EM-370(5), IT-150G. These materials can pass 4 times sequential lamination. They are also suitable for HDI and buried via hole products.
Consider the thermal performance for halogen free material. The prior recommendation is R-1566(WN). Thermal performance of R-1566(WN) is the best among these middle Tg material.
The price of material is related to volume of buying. Some factories provide price of mid-Tg as lower as normal Tg, while some factories would quote same price between high-Tg and mid-Tg.
Key parameter list for this example:
Type | Tg (°C) | Maximum layer count | T288 (min) | Maximum Sequential lamination times | Shorter LT/ easier to purchase? | Price competitive |
---|---|---|---|---|---|---|
S1000H (Shengyi) | 160 | 16 | 20 | 4 | Y | Good |
IT-158(ITEQ) | 155 | 16 | 30 | 4 | Y | Good |
IT-150G(ITEQ) | 155 | 16 | 60 | 4 | Y | Good |
EM-370(5) (EMC) | 150 | 16 | 60 | 4 | N | Pair |
R-1566(WN)/R-1551WN ( Panasonic) | 148 | 16 | >30 | 4 | N | Pair |
Type | Tg (°C) | Maximum layer count | T288 (min) | Maximum Sequential lamination times | Shorter LT/ easier to purchase? | Price competitive |
---|---|---|---|---|---|---|
S1000H (Shengyi) | 160 | 16 | 20 | 4 | Y | Good |
IT-158(ITEQ) | 155 | 16 | 30 | 4 | Y | Good |
IT-150G(ITEQ) | 155 | 16 | 60 | 4 | Y | Good |
EM-370(5) (EMC) | 150 | 16 | 60 | 4 | N | Pair |
R-1566(WN)/R-1551WN ( Panasonic) | 148 | 16 | >30 | 4 | N | Pair |
To conclude, there are multiple variables to look at when selecting a material for your design. If you are designing a PCB and are unsure which materials will be best for your product, please contact us and we can help you select the right material. This can also help us streamline the production and get the boards to you faster.